"Green transformation X digital operation": Wistron Hwa-Nan Plant selected as a "Lighthouse Factory"
2023.04.20
News
The "Lighthouse Factory", selected by the World Economic Forum (WEF) in partnership with McKinsey, is hailed as the "most advanced factory in the world" and serves as a model for "digital manufacturing" and "globalization 4.0", representing the highest level of intelligent manufacturing and digitalization in the global manufacturing industry. Since 2018, only 132 factories worldwide have been awarded this honor. On January 13, 2023, the WEF officially announced the latest list of "Lighthouse Factory", and Wistron Hwa-Nan Plant was successfully selected, becoming the second plant of Wistron to receive the title of "World Lighthouse Factory".
During the on-site evaluation, the expert group visited Wistron Hwa-Nan Plant's Digital Capability Center (DCC) and Zhongshan Plant 3. We presented examples to the expert group from multiple dimensions such as business scenarios, pain points, technical solutions and details, and technical application benefits. We received high recognition from the expert group, especially for the operation of the DCC and its achievements in promoting the company's digital transformation.
Wistron Hwa-Nan Plant's successful selection as a "Lighthouse Factory" is not only due to the excellence in every aspect of the manufacturing process, but also the introduction of multiple leading digital technologies in the industry, which has in turn achieved cost reduction, efficiency improvement, and increased production scale. Moreover, it has effectively reduced energy consumption and achieved outstanding results in low-carbon development. To meet the demand for high-quality delivery of 60% of orders within 72 hours, the plant reconstructed the entire value chain through 33 self-developed digital use cases, achieving a 32% increase in UPPH (Units Per Hour Per Person), a 55% reduction in product defect rate, and overcoming the difficulties caused by material shortages to shorten product delivery time to 48 hours. Eventually, the manufacturing cost of a single product was reduced by 22%. The energy management system saved a total of 8.02 million US dollars, resulting in a 41% reduction in product energy consumption, a 33% decrease in electricity usage, and a 37% reduction in carbon emissions. The solar power station generates 5.5 million kWh of electricity annually, reducing carbon emissions by 4,423 tons.
Envisioning the future with the present in mind, we will leverage the success of being selected as a Lighthouse Factory to accelerate our digital transformation and propel our digital operations to new heights. We will strive towards sustainability through innovation, and constantly enhance our leading position on the global stage.
During the on-site evaluation, the expert group visited Wistron Hwa-Nan Plant's Digital Capability Center (DCC) and Zhongshan Plant 3. We presented examples to the expert group from multiple dimensions such as business scenarios, pain points, technical solutions and details, and technical application benefits. We received high recognition from the expert group, especially for the operation of the DCC and its achievements in promoting the company's digital transformation.
Wistron Hwa-Nan Plant's successful selection as a "Lighthouse Factory" is not only due to the excellence in every aspect of the manufacturing process, but also the introduction of multiple leading digital technologies in the industry, which has in turn achieved cost reduction, efficiency improvement, and increased production scale. Moreover, it has effectively reduced energy consumption and achieved outstanding results in low-carbon development. To meet the demand for high-quality delivery of 60% of orders within 72 hours, the plant reconstructed the entire value chain through 33 self-developed digital use cases, achieving a 32% increase in UPPH (Units Per Hour Per Person), a 55% reduction in product defect rate, and overcoming the difficulties caused by material shortages to shorten product delivery time to 48 hours. Eventually, the manufacturing cost of a single product was reduced by 22%. The energy management system saved a total of 8.02 million US dollars, resulting in a 41% reduction in product energy consumption, a 33% decrease in electricity usage, and a 37% reduction in carbon emissions. The solar power station generates 5.5 million kWh of electricity annually, reducing carbon emissions by 4,423 tons.
Envisioning the future with the present in mind, we will leverage the success of being selected as a Lighthouse Factory to accelerate our digital transformation and propel our digital operations to new heights. We will strive towards sustainability through innovation, and constantly enhance our leading position on the global stage.
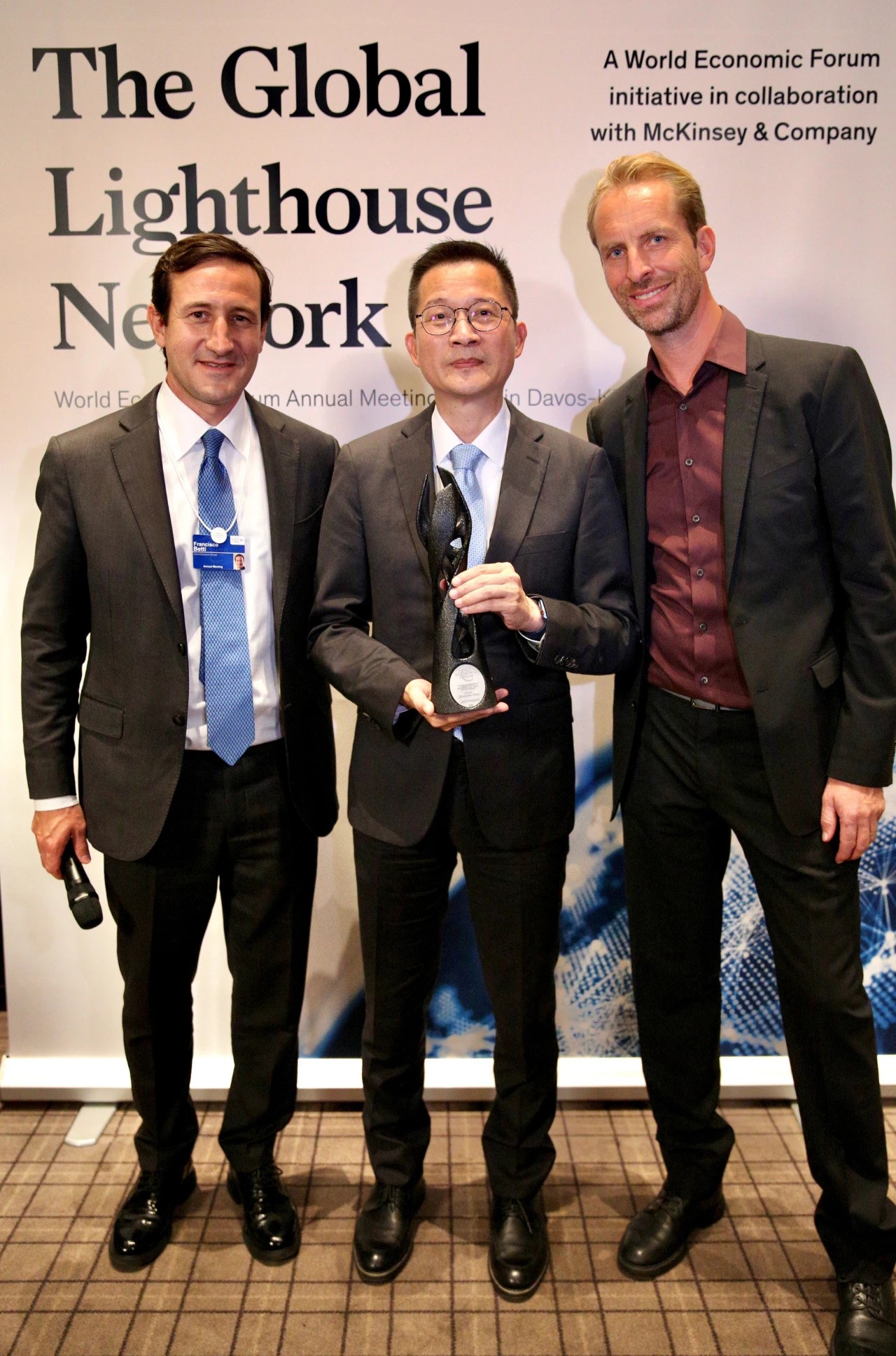