Occupational Safety and Health Policy and Targets
As a leading technology service provider in the global ICT industry, Wistron strives to become world-class enterprise by ensuring a healthy, injury-free environment, reducing the impact and risk on stakeholders via the following commitments and actions. In addition to policy advocacy, we appoint dedicated units to supervise the occupational safety and health management of each site and carry out occupational safety and health management activities. In accordance with the company's occupational safety and health policy, each plant sets its own performance targets. The overall goal of the company is to achieve zero significant occupational incidents (where a significant occupational incident is defined as a fatal accident).
Wistron places great importance on maintaining a safe and healthy workplace environment for employees and continuously strives to identify and mitigate potential occupational safety and health risks.
The Company's overall targets: 0 major work safety incidents
Occupational health and safety management system
Wistron's plants leverage ISO 45001 Occupational Health and Safety Management System to maintain effective operations. Through education, training, promotion, and drills, the company ensures that all stakeholders have a clear understanding of their safety and health obligations and rights. This proactive approach aims to reduce and eliminate risks and impacts related to occupational safety and health.
Site |
Original Issue Date |
Expiration Date |
Neihu Headquaters / Hsichih Office Complex / Hsinchu Plant / Hukou Plant |
2024/4/30 |
2027/5/11 |
Chongqing Plant |
2024/9/8 |
2027/10/9 |
Chengdu Plant |
2022/7/27 |
2028/08/10 |
Automotive Electronics Kunshan Plant |
2024/5/9 |
2027/5/8 |
Zhongshan Plant |
2024/8/30 |
2027/10/8 |
Mexico Plant |
2022/8/29 |
2025/7/15 |
Czech Plant |
2023/3/10 |
2026/3/13 |
KOE Plant |
2022/10/20 |
2025/10/19 |
Vietnam Plant |
2025/2/18 |
2028/2/18 |
Malaysia plant |
2024/6/24 |
2027/4/24 |
Labor Safety Committee
All Wistron plants have established a Labor Safety Committee to facilitate communication, provide consultation, and respond to complaints. The members of the Committee include managers responsible for decision-making as well as labor representatives. They serve to provide communication channels for employee participation and consultation in occupational safety management systems. Employees can offer their thoughts or suggestions on occupational safety and health to department representatives who will share employee feedback during annual meetings, allowing our employees to communicate with senior executives through the Committee.
Occupational Safety and Health Measures
Hazard Identification
|
- Regular environmental hazards risk assessments to assess whether the operating procedures comply with regulations
- The Company requires corrections for non-compliant procedures in accordance with legal requirements and tracks improvement through internal regulations
|
Communication and engagement
|
- Labor Safety Committee
- Internal communication, consultation, and complaint procedures
|
Health Protection
|
- Employee health check plan,and Including employees working at special positions (e.g., high-noise, dust, and X-ray, etc.)
- Regular inspections of operational environments
- On-site medical rooms, doctor visits, and counseling services
|
Training and education
|
- Safety and health education and training for new employees
- Special hazard or first aid trainings for specific operators
- Annual Occupational Safety and Health Management System officer training program
- Health seminars and speeches from experts to answer employees' health questions
|
Emergency Response
|
- In 2024, a total of ten courses have been arranged for multi-scenario escape and evacuation simulation drils (daytime/nighttime, earthquakes, and fire disasters)
- In 2024 a total of 53 response drills have been arranged for infrastructure emergencies (fire safety and elevators)
- In 2024, a total of 25 courses have been arranged for emergency first aid and responders training
|
Protection measures
|
- Rigorous application and control regulations for specific operators (e.g., soldering, usage of chemicals, and loud environments) and formulation of corresponding control plans or measures according to risk assessment
- Continuous improvement of occupational safety and health management systems
- Require the use of personal protection equipment
|
Supplier Management
|
- When new suppliers are introduced, the Company verifies that they meet the basic requirements for occupational safety and health management system certification
- Regular supplier audits include items on occupational safety and health management. In 2024, WHQ/ WIH adopted the ISO 20400 Sustainable Procurement Guidance
|
Internal audit
|
- Regular internal audits at least once a year for timely improvement measures against non-conformities; audit reports provided to relevant management units
- In cases involving personnel-related deficiencies, hazard identification and elimination processes are implemented, alongside strengthened awareness campaigns and training programs
|
Education and Training on Occupational Safety and Health
To ensure employees fully understand Wistron's occupational safety and health regulations and management system, and are equipped to respond to hazards and accidents, we conduct annual audits involving on-site inspections and verification activities. Additionally, all new employees are required to undergo general introductory education courses, such as Responsible Business Alliance (RBA) training.
For employees in specific job positions where unique hazards may occur, tailored specialized training is provided. This includes hazard notification training at the Malaysia plant and emergency response drills at the Czech plant, which focus on strengthening employee safety awareness and validating the safety of the working environment.
In 2023, a total of 200,106 individuals completed training, accumulating 168,406 training hours. Each plant conducts regular emergency response training and establishes relevant reporting processes tailored to its specific characteristics. This ensures the effectiveness of organizational disaster recovery mechanisms and reduces false alarms. In 2023, there were 51 reported For historical data, please refer to the section on internal near miss incidents.
|
2023 |
2024 |
Training (people) |
200,106 |
153,659 |
Training (hours) |
168,406 |
151,447 |
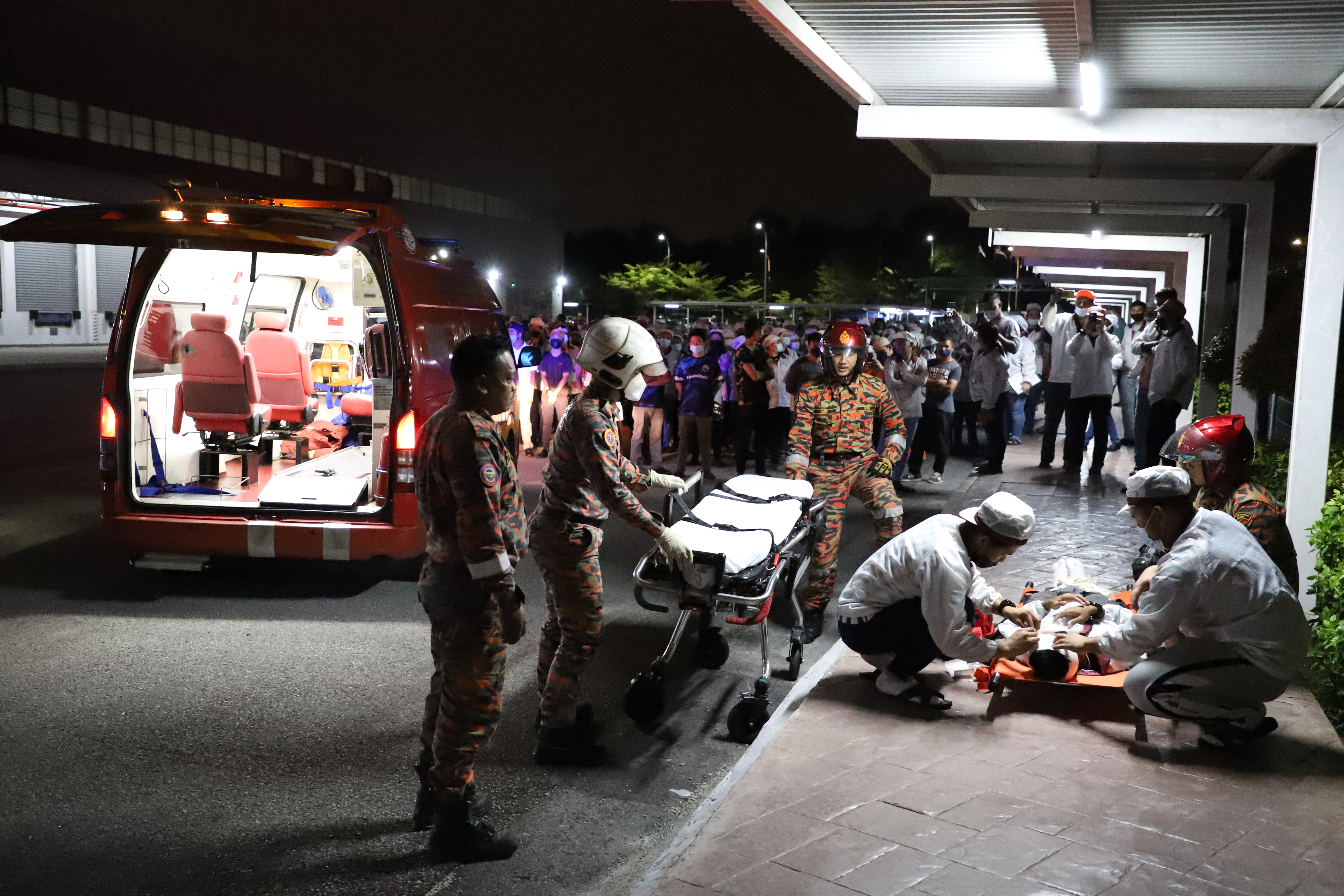
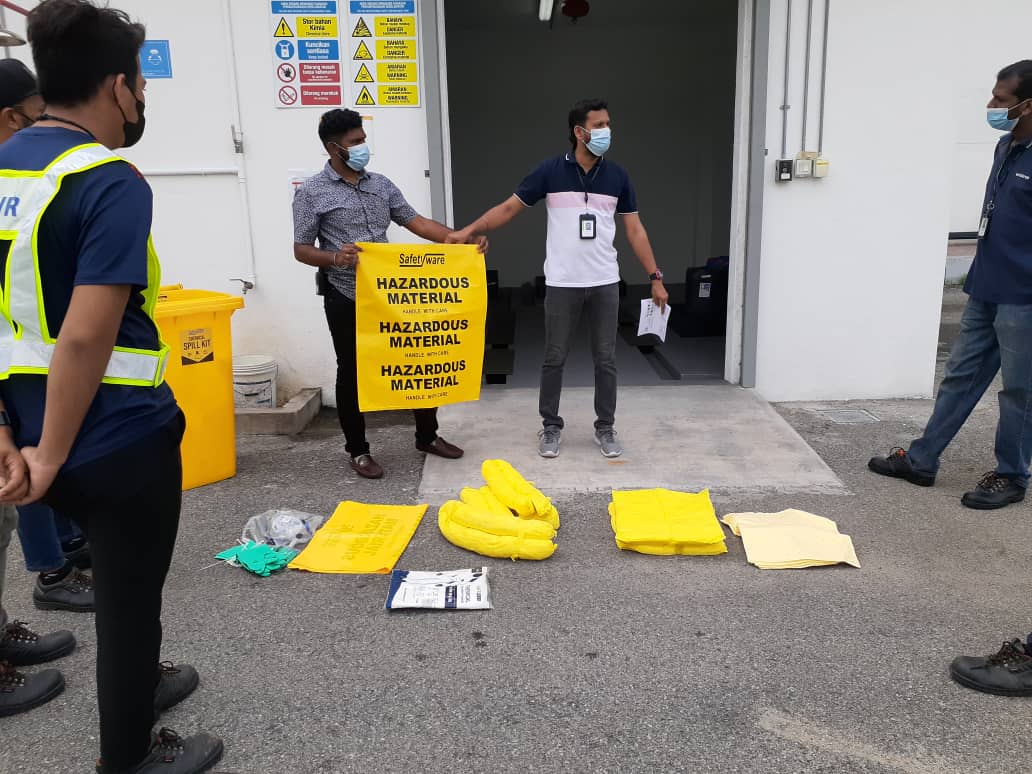
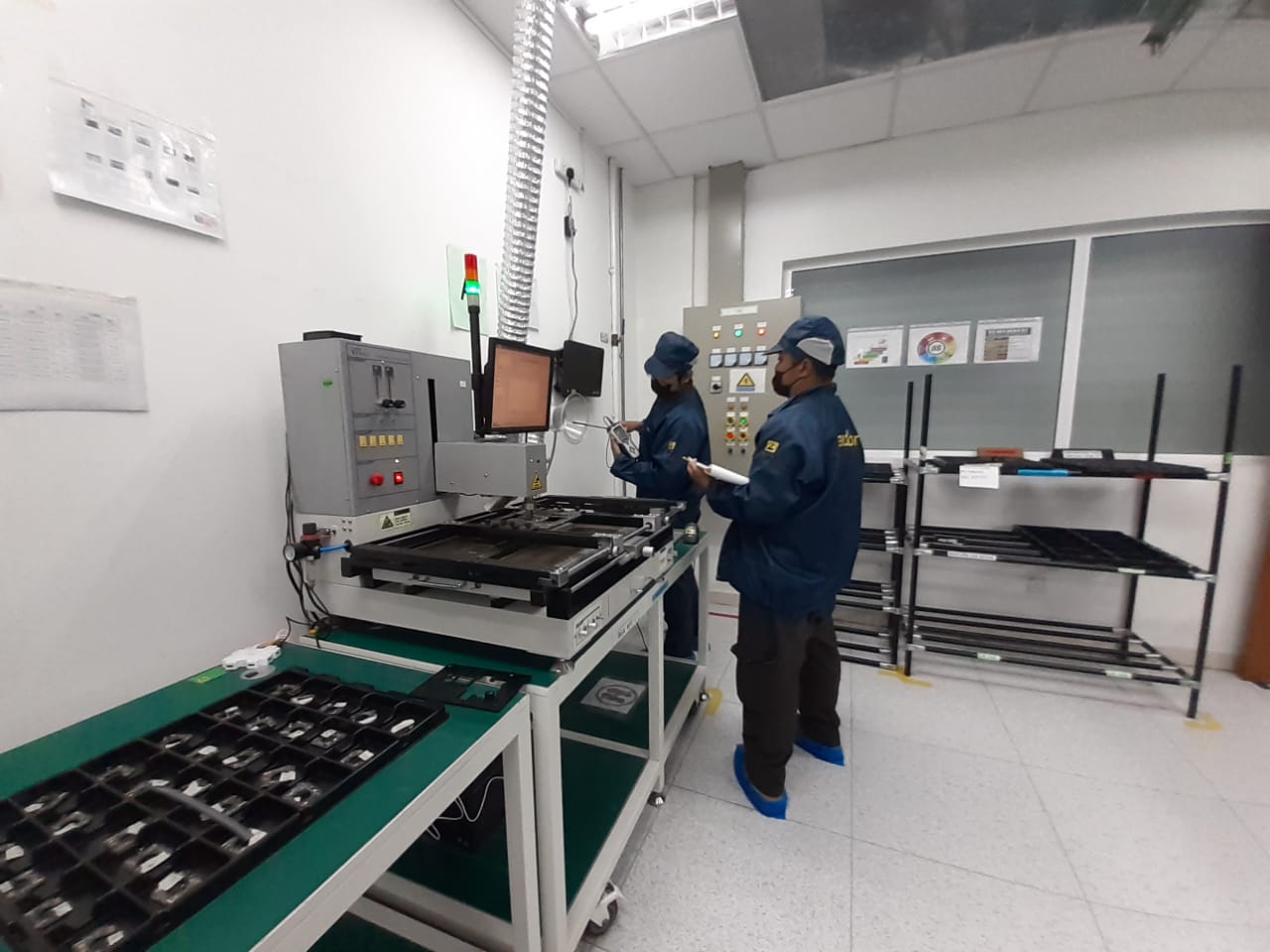
▲
Night-time emergency first aid drill ▲
Hazardous substance awareness training ▲
Exhaust system functionality test
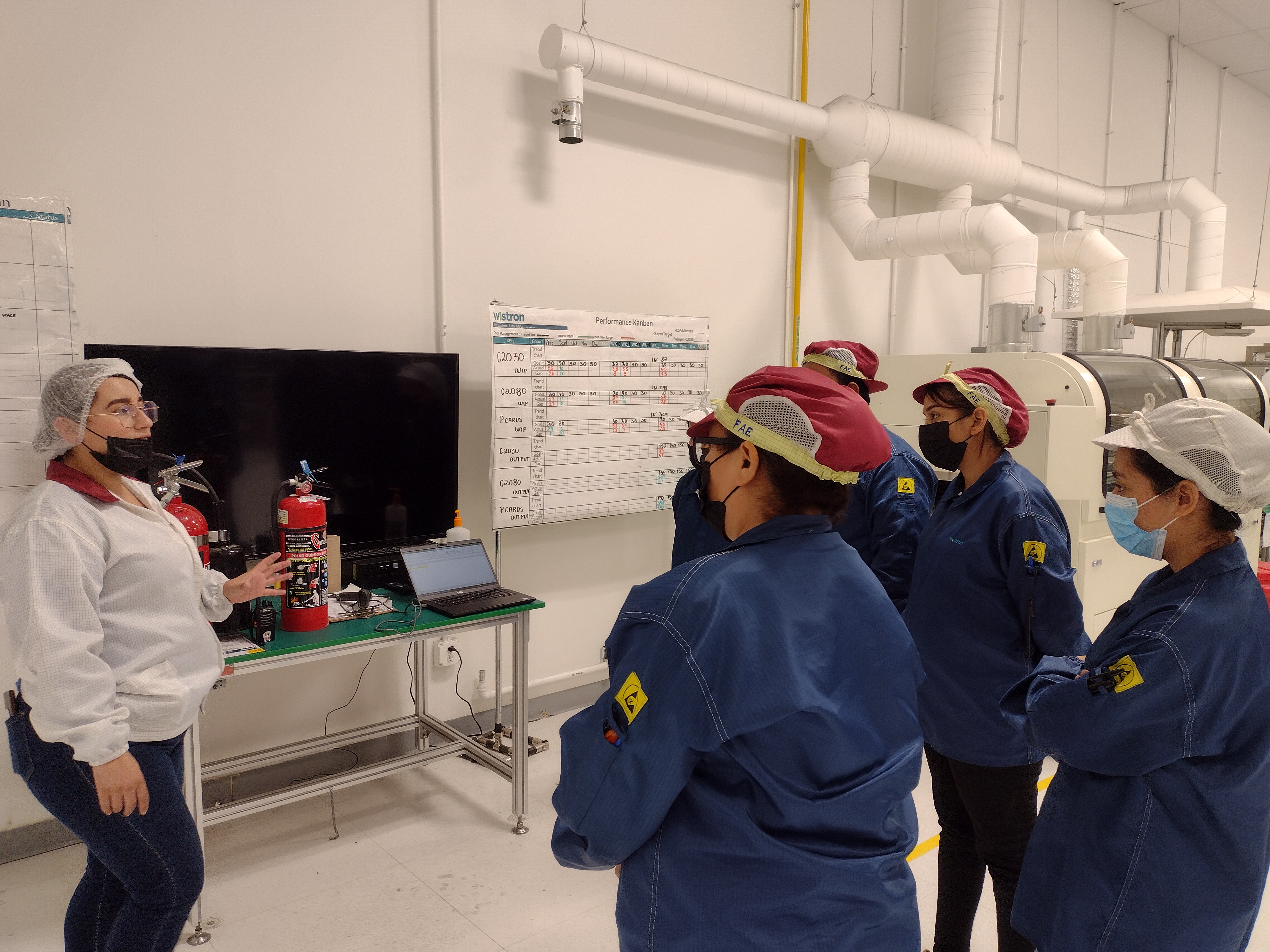
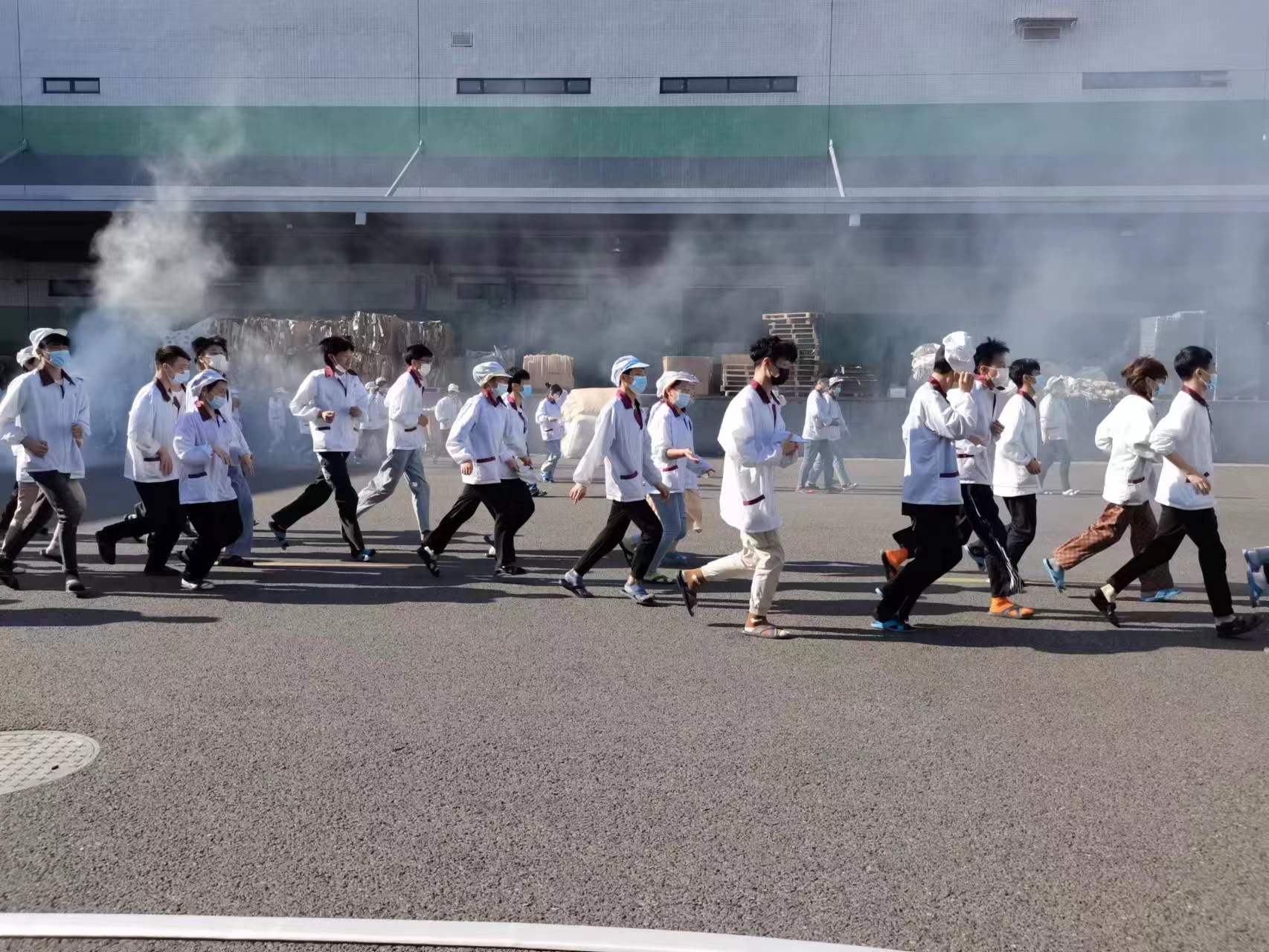
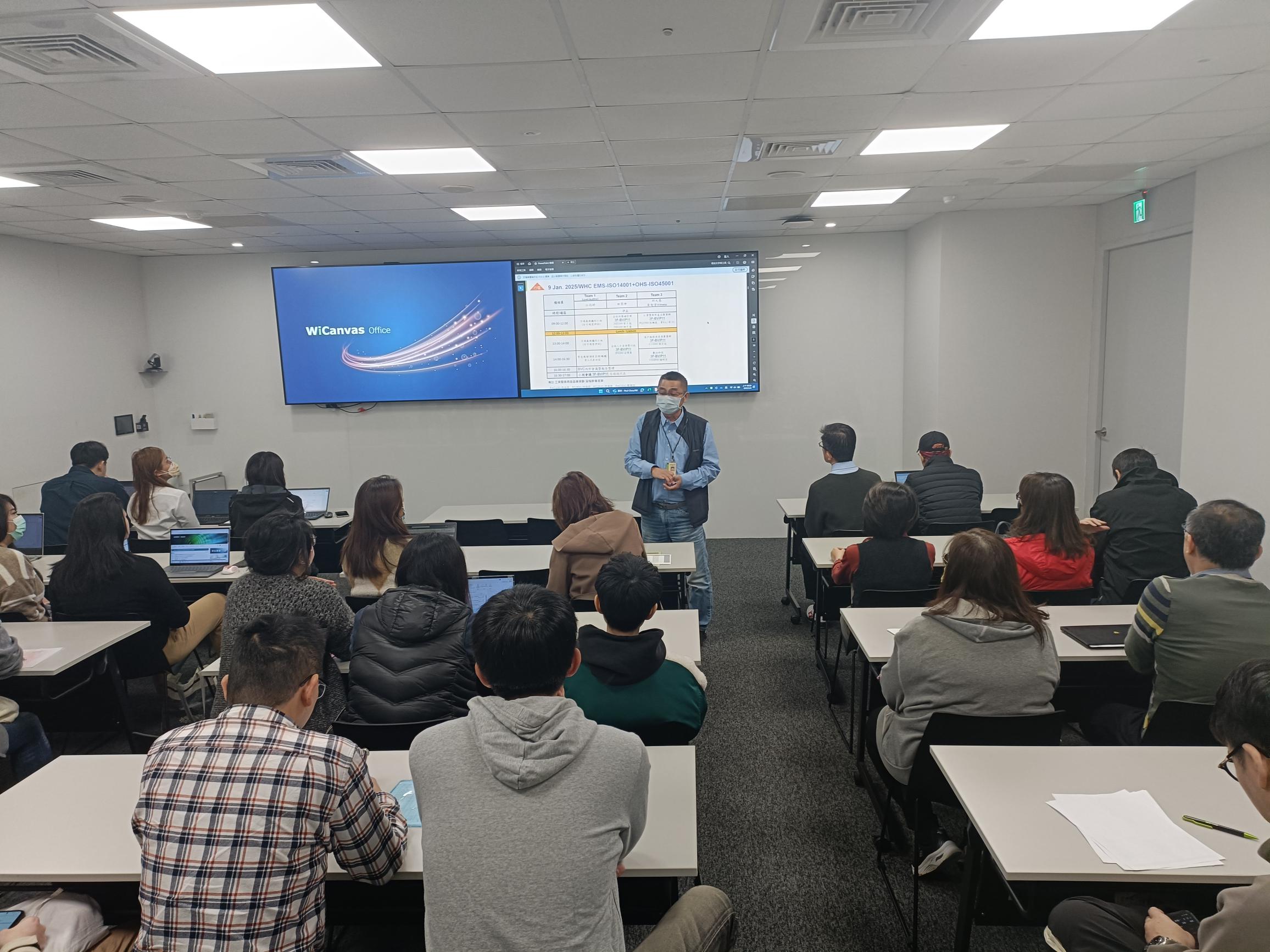
▲
Fire drill ▲
Emergency evaluation drill ▲
Annual ISO 45001 audit
Hazardous Substance Management
Trained and qualified professionals are tasked with overseeing the management of hazardous chemicals used in manufacturing processes. Comprehensive controls are in place for the procurement, handling, storage and use of hazardous chemicals. In 2024, the environmental protection action of the Taiwan plant has been carried out to completely replace the environmentally friendly cleaners that mainly use petrochemical detergents, and continue to reduce the environmental impact. Additionally, an annual safety and health training plan is regularly held to provide personnel with operational trainings, emergency response protocols, and educational training. SDS (Safety Data Sheet) is also displayed in accessible areas for on-site operators to consult when needed for effective response in the event of emergencies.
Workplace Hazard Identification and Risk Assessment
Trained and qualified personnel in identifying hazards and using quantified risk factors as the basis for risk assessment. Following review by the occupational safety and health management unit, risk levels are established, and operational controls and improvement objectives for hazard risks are defined. These are tracked regularly within the occupational safety and health management system to ensure potential occupational hazards are being consistently eliminated from the workplace.
In the event of an immediate and dangerous emergency during any operation, employees are authorized to assess the situation based on the severity of the danger present and then determine whether to cease operations or take necessary protective measures before evacuating without adverse consequences. In 2024, we continued to monitor occupational safety risk indicators - ≤1.14‰. Risks are mitigated through regular training and monitoring mechanisms. Monthly controls and tracking of facility indicators are carried out to minimize the likelihood of risk occurrence. No related risks were identified in 2024.
Most medium-to-high-risk items pertain to mechanical injuries caused by improper handling of equipment. To mitigate this, employees are subject to additional training to ensure proper use of personal protective equipment and workflow inspections to reduce the likelihood of incidents.
Voluntary Reporting of Near Miss Incidents
Wistron has SOPs in place for near-miss incidents, such as fire, power outages or earthquakes. They are reported to the responsible units in accordance with the Incident Response and Investigation Management Procedures to verify whether an incident has occurred, conduct investigations, track events, and promote safety and health. Each incident is then documented in a near-miss incident record, submitted to superior officers and then retained for reference. The Company analyzes the causes, formulates corrective and preventive measures, evaluates the effectiveness of these measures, and continues to monitor improvement efforts.
Wistron has designed online platforms such as Columbus, an internally trained knowledge base, to facilitate prompt communication. It includes an intelligent customer service module to address inquiries from employees. Additionally, internal communication procedures are in place to facilitate quick reporting of any emergencies or near miss incidents.
In 2024, there were a total of 58 near miss incidents. The majority of near miss incidents were caused by equipment and facility malfunctions or negligence, such as false fire alarms. Prompt action and subsequent measures were taken to verify the functionality of related equipment and enhance inspection procedures, respectively. Specific maintenance precautions are also included to prevent similar incidents in the future.
Data on Occupational Hazards & Injuries
Wistron identifies occupational safety and health issues with potential risks by analyzing data on occupational hazards and injuries, which guides the formulation of specific action plans to improve workplace safety and reduce work-related injuries. Work-related injury statistics for Wistron employees and non-employee workers in 2024 are shown in the table below. Each plant reports detailed information on work injuries by month, as well as monitoring and tracking by designated personnel to ensure they stay informed about work injury management. The tables below are compiled based on legal reporting requirements, with a focus on recording injuries. The definition of severe occupational injuries follows government regulations. We have not received any reports on occupational diseases. In terms of managing non-employee workers, all Wistron plants comply with local regulations in managing on-site personnel and subcontractors. Through vendor selection and contractor management, Wistron assesses and standardizes operational standards for suppliers to achieve our expected results from occupational safety and health management systems. In 2024, no significant violations (defined as violations with ≥NT$1M fines) occurred in the management of subcontractors.
In 2024, work-related injuries in Taiwan and Asia decreased from last year, primarily due to a reduction in moderate and severe accident incidents, which were mostly related to traffic accidents during commuting. The administrative units have continued to enhance communication on traffic safety and personal safety awareness and training in the office areas through bulletin boards.
In contrast, the number of lost workdays in Europe and the U.S. increased compared to last year, mainly due to light injuries, most of which are mechanical injuries caused by improper actions. To address this, Wistron has strengthened employee education and training, and has reviewed standard operating procedures to ensure that all employees wear protective equipment to prevent injuries.
Occupational Injury Statistics of Employees
Occupational Injury Statistics of Workers Other Than Employees
Statistics of Disabling Injuries |
Taiwan |
Asia (excluding Taiwan) |
Europe and Americas |
Year |
2021 |
2022 |
2023 |
2024 |
2021 |
2022 |
2023 |
2024 |
2021 |
2022 |
2023 |
2024 |
Total Work Hours |
17,929,115 |
22,693,604 |
23,387,274 |
24,500,263 |
112,417,169 |
102,076,209 |
65,965,432 |
67,207,272 |
9,826,451 |
17,697,391 |
5,195,678 |
8,337,833.3 |
Main Category of Occupational Injury |
Traffic accident |
Traffic accident |
Traffic accident |
Traffic accident/Fall |
Traffic accident |
Traffic accident |
Machine-related injury |
Machine-related injury |
Machine-related injury |
Machine-related injury |
Machine-related injury |
Machine-related injury |
Crush injury due to mishandling of objects |
Falls |
Number of work-related injury cases |
60 |
75 |
73 |
73 |
47 |
43 |
21 |
20 |
35 |
30 |
18 |
97 |
Occupational Injury Rate |
0.67 |
0.66 |
0.62 |
0.60 |
0.08 |
0.08 |
0.06 |
0.06 |
0.71 |
0.34 |
0.69 |
2.33 |
Occupational Disease Rate |
0 |
0 |
0 |
0 |
0 |
0 |
0 |
0 |
0 |
0 |
0 |
0 |
Lost Day Rate |
3.49 |
4.73 |
6.85 |
4.74 |
0.95 |
3.53 |
4.97 |
3.03 |
12.35 |
0.69 |
12.59 |
16.89 |
Total Number of Work-Related Fatalities |
0 |
0 |
0 |
0 |
0 |
0 |
0 |
0 |
0 |
0 |
0 |
0 |
- Note1 : Occupational injury rate (IR): (Number of occupational injury incidents/total work hours) * 200,000 (Calculation for light injuries: Only Czech/Mexico/Philippines/U.S./Hukou Plants include light injuries in their IR, all other plants exclude light injuries).
- Note2 : Occupational disease rate (ODR): (Total occupational disease cases/total work hours) * 200,000.
- Note3 : Lost day rate (LDR): (Number of lost days due to work injuries/total work hours) * 200,000 (calculation of days: all plants calculate days based on scheduled workdays).
- Note4 : In the Czech Republic, employees may visit doctors during work hours (unlimited visits covering journey time as well), and they may also stay at home to rest for a longer period of time when sick.
- Note5 : Scope: All full-time employees.
- Note6 : According to corporate ESG information disclosure regulations and the definition of relevant occupational accident data of Taiwan Stock Exchange Corporation (the “TWSE”), the percentage of occupational accidents is 0.064%.
Statistics of Disabling Injuries |
Taiwan |
Asia (excl. Taiwan) |
Europe & Americas |
Year |
2021 |
2022 |
2023 |
2024 |
2021 |
2022 |
2023 |
2024 |
2021 |
2022 |
2023 |
2024 |
Number of people |
101 |
190 |
221 |
233 |
1,716 |
2,165 |
1,718 |
1,779 |
1,544 |
648 |
234 |
479 |
Total Work Hours |
220,562 |
394,284 |
421,882 |
483,986 |
3,934,312 |
6,750,594 |
3,709,626 |
3,294,392.9 |
247,239 |
205,123 |
606,000 |
1,037,094 |
Main Category of Occupational Injury |
None |
None |
None |
None |
None |
Crash |
Pinch |
Machine-related injury |
None |
Fall over |
Cut |
Machine-related injury |
Number of work-related injury cases |
0 |
0 |
0 |
0 |
6 |
5 |
1 |
3 |
3 |
1 |
1 |
6 |
Occupational Injury Rate |
0 |
0 |
0 |
0 |
0.31 |
0.15 |
0.05 |
0.18 |
2.43 |
0.98 |
0.33 |
1.16 |
Occupational illness Rate |
0 |
0 |
0 |
0 |
0 |
0 |
0 |
0 |
0 |
0 |
0 |
0 |
Lost Day Rate |
0 |
0 |
0 |
0 |
0 |
0.83 |
0.02 |
0.61 |
11.33 |
68.75 |
0.17 |
18.9 |
Total Number of Work-Related Fatalities |
0 |
0 |
0 |
0 |
0 |
0 |
0 |
0 |
0 |
0 |
0 |
0 |
- Note: Scope of the number of people in the survey as of December 31: Work personnel of plants: security guards, cleaners, kitchen/cafeteria personnel, and others (long-term onsite operators and specialists)
Employee Absence Rate
Note 1 : Absence Rate: Number of absent days/Number of days to work*100. The number of days to work: refers to the number of working days. The number of working days is the sum of the total annual working days of each plant around the world.
Note 2: Sick leave excludes leave taken due to the pandemic.
Note 3: The target value of absenteeism rate in 2024 was set at 1.04 (set to not exceed the average value of the previous three years).
Accident Investigation
When an employee or a contractor experiences a work safety incident, Wistron will investigate the incident and track progress in accordance with the Accident Response and Investigation Management Procedures. Then, we will determine damage conditions and occupational injuries based on the accident. After the accident investigations are completed, the Company is required to submit the results and carry out response measures for the designated supervisory unit to oversee and track to reduce losses and prevent similar situations in the future.
In 2024, Wistron's Hsinchu plant in Taiwan experienced one fire incident caused by the outdoor air conditioning unit burning out, which only affected a small part of production. All our operational locations have property insurance coverage, and this incident did not have any significant impact on overall operations or finances. Although no injuries or casualties occurred, the company has conducted a thorough review of the contractor management mechanisms during the new plant construction phase to prevent recurrence of such incidents.
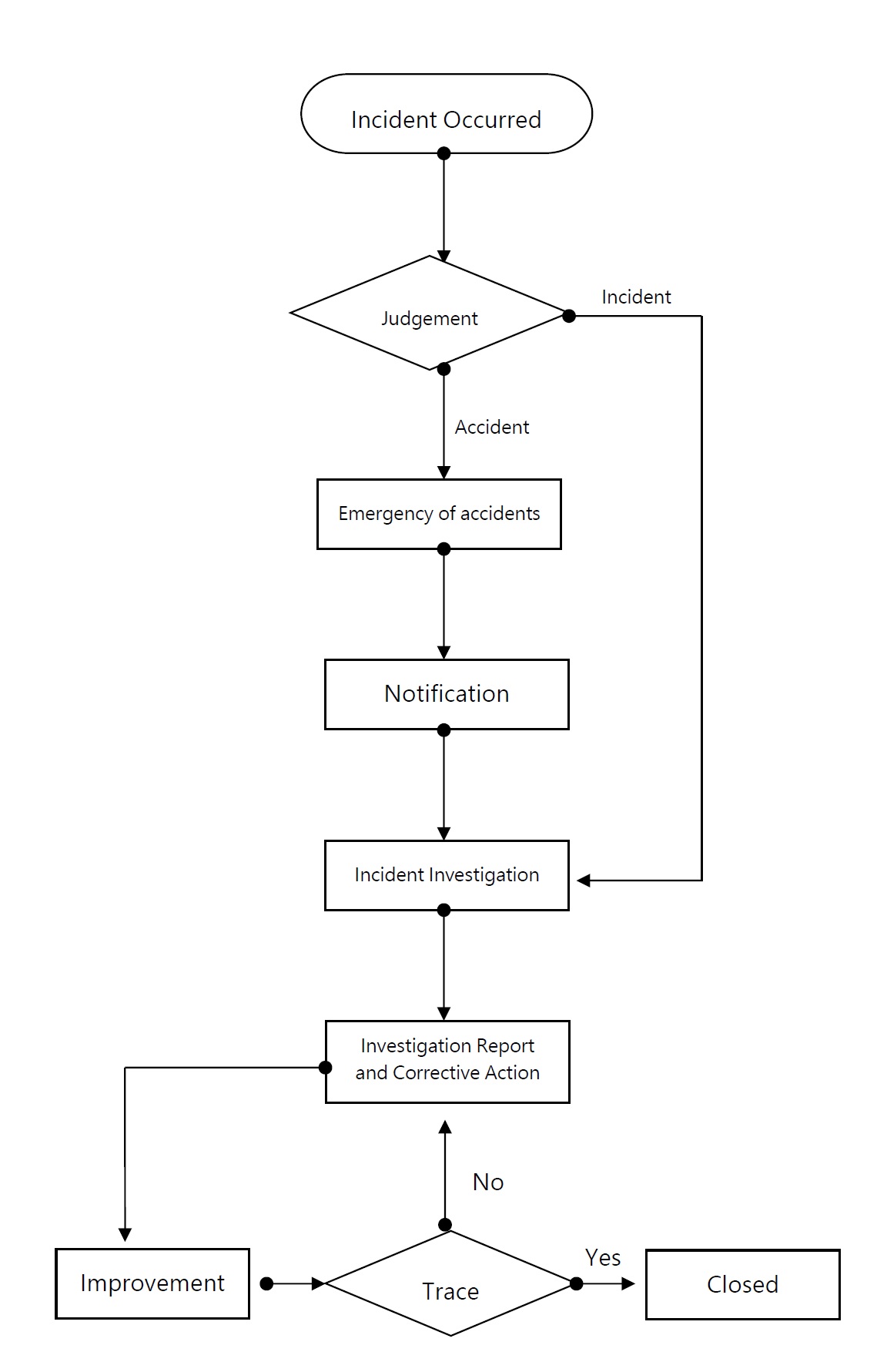